“Let us tread
lightly on the planet so that our children
and grandchildren can
follow in our footsteps.” [1]
|
1. INTRODUCTION
Sustainability is about living now in a way that
does not compromise future generations - not only of humans, but
also of the other life forms with which we are interdependent. It
requires us to be aware of the potential that humans have to upset
planetary balances and to deplete irreversibly the resources on
which we depend. We are having to reconsider many of our activities
in order to find less environmentally-damaging ways in which to
live.
In recent years, the shipping industry has
enjoyed growth as it successfully responded to the commercial
pressures for more rapid, reliable, and economic distribution of raw
materials and products. However, the industry is now being asked to
become more sustainable in its operation. At the recent Copenhagen
summit on climate change, the International Maritime Organisation
recognised the need for commercial shipping to reduce emissions,
possibly by as much as 50% by 2050 [2]. This significant reduction
will have to be achieved during a period when the demand for
shipping is projected by the Ocean Policy Research Foundation (OPRF)
of Japan to increase by a factor of 2.5 [3].
Although there is widespread awareness of
sustainability issues within the maritime industry, there are
concerns that the response so far has been too slow [3]. The
required changes will not be easy, particularly since the evidence
and interpretations relating to human impact on the environment and
biodiversity are still incomplete and inconclusive. The UN
Intergovernmental Panel on Climate Change (IPCC) has reported a
scientific consensus that greenhouse-gas emissions resulting mainly
from the burning of fossil-fuels have been a major contributor to
recent global warming and precipitation changes [4]. At the same
time, the IPCC acknowledges that fundamental gaps exist in our
knowledge [reviewed in 5]. Climate-change sceptics highlight these
uncertainties and it is perhaps not surprising therefore that there
is reluctance within the shipping industry at this time to take what
may appear to them to be costly steps into the unknown. It is
possible that commercial pressures still outweigh sustainability
considerations.
Most commercial ships have to meet tight
operating schedules when moving materials around the world, and wind
power alone would be unable to meet these requirements given the
variable nature of the wind and its uneven distribution across
global shipping routes. For this reason, wind power alone is
commercially viable only for certain types of cargo for which a
longer transit time is not a disadvantage [20]. For other
time-dependent cargoes, it is more practical to use wind power as a
form of assistance to engine-power.
The focus in this paper is the provision of wind
assistance to certain types of ships – those with sufficient areas
of open deck space - by add-on sail modules. Sail modules will allow
vessels to throttle back their engines in order to conserve fuel and
reduce harmful emissions.
To some ship owners and operators, the proposal
to fit sails to commercial ships might be seen as a retrograde step,
and imply the need for more crew, greater risk to crew members,
increased dependence on specialised weather knowledge, costly
vessels vulnerable to storm conditions and awkward to manoeuvre in
port, and erratic performance in relation to schedules. The purpose
of the following proposal is to allay at least some of these
misgivings, and show that in addition to environmental benefits
there are also potential commercial benefits from wind assistance.
2.
CRITERIA FOR PRACTICAL WIND ASSISTANCE
For wind to become once again a significant
source of propulsion for commercial shipping operating in the
contemporary commercial context, several key requirements will need
to be met. These were identified in a major study of the issues
relating to wind power for larger ships initiated in 1995 by the
Danish Government and carried out by Knud E Hansen [21, 22]. To be
effective under today’s conditions, sailing rigs for commercial
ships:
-
need to be operational without the
need for more crew
-
must not endanger the crew
-
must not interfere with cargo
handling
-
must not jeopardise the safety of
the vessel
-
must be reliable with the minimum of
maintenance
-
must work well when sailing upwind
-
must not exceed 60m mast height (a
limit imposed by the Panama Canal and some harbours)
-
should not obscure visibility during
manoeuvring
-
ideally should be suitable for
existing ships.
|
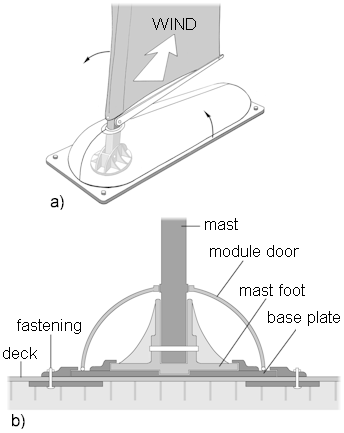
Figure 3: a) tilting forces generated
by the rig; b) a schematic cross-section through the base of the
rig showing the relationship between the mast foot, base plate,
and deck.
|
4.2 CHALLENGES PRESENTED BY THE SAIL
MODULE CONCEPT
The main engineering problem associated with the
sail module approach will be to dissipate the sailing forces
generated by the rig without having the benefit of a mast that
penetrates deep into the ship’s structure. Stays and shrouds which
are used in traditional rigs to give added support to the mast would
not be applicable here given the folding, rotating nature of the
rig. The base plates of the sail modules will have to disperse the
forces into the deck and its substructure. Whichever is the windward
side of the base plate will have a tendency to lift from the deck,
so the anchorage points will have to be able to resist this force
(Figure 3).
(There are parallels here
with the situation faced by trees. Contrary to popular belief, the
root systems of 80-90% of trees have shallow root systems within the
top 60cms of the soil to resist the toppling forces produced by the
wind [26].) The module doors, when closed, could provide some
additional buttressing to the lower segment of the mast whilst still
allowing it to turn within a bearing. Given the stresses involved,
it is probable that the deck will need additional reinforcement in
the area of module attachment.
Unlike fixed standing
rigging, folding rigs have the advantage that they can be protected
from extreme conditions by being stowed in their protective pods,
and only deployed when forces lie within the range that the module
has been designed to withstand. If an acute situation arises that
overwhelms a sail module while it is in use, or if the safety of the
vessel is being threatened, there is also the potential to release
the module from its fastenings and sacrifice it from the ship.
The mechanisms producing
extension, folding, rotation of the mast, and opening and closing of
the module doors, together with their control systems, will be
comparable to those already in widespread use in equipment such as
cranes and derricks.
Existing ships will need
modification before the sail modules could be attached. This will
probably involve repositioning of some equipment to clear suitable
areas of deck space, reinforcement of the deck beneath the modules,
locking devices to hold the base plate securely to the deck, and
links with the ship’s hydraulic, electrical, and control systems.
For ships with more limited deck space, for example bulk carriers
with midline hatches, it may be feasible to cantilever the pods
partially out from the sides of the ships so that they do not
obstruct loading and unloading. All of these structural changes will
have a cost penalty, and this will need to be recouped from the fuel
savings provided by the sail modules over a reasonable operating
period.
With wind assistance, a ship
will be able to throttle back its main engine(s). This may result in
the engine and/or propeller working sub-optimally. Laboratory
research and experience at sea will be required in order to find
ways of balancing the sails, engine(s), and propeller(s) in
particular cases to obtain the greatest benefit from wind
assistance.
In recent years there has
been considerable progress in the understanding of the aerodynamics
of sails. There has for example been rapid evolution in the design
of windsurfing sails which because of their small scale have lent
themselves to experimentation. This experience has subsequently
influenced sail design at larger scales, for example in the
America’s Cup. This progress in understanding will provide a
valuable resource when developing sails for larger vessels.
Multiple sails in proximity to each
other interact, so obtaining optimal performance from multiple sail
modules on a single vessel will require testing and experience. The
interactions depend on the direction of the apparent wind, so that
on some points of sail the rigs might facilitate each other while on
other points of sail there may be wind shadowing of rigs to leeward.
To develop a better understanding of the aerodynamics and control of
multiple rigs, a dinghy was modified to accept 3 rigs of a similar
design to the one proposed for the sail modules and tested on the
water [27].
4.3 ENCOURAGING THE
UPTAKE OF SAIL MODULES
In addition to finding
solutions to the engineering challenges described above, it will be
necessary to convince the shipping industry that the adoption of
wind assistance makes commercial sense. Ship operators face two main
categories of risk if they decide to invest in wind assistance [28]:
-
operational risk,
including risk of damage to the ship’s structure, risk of
capsize, risk of not keeping to schedule, risk to crew members,
and risk of not complying with existing legislation
-
financial risk,
including cost of purchase, cost of maintenance, reliability of
revenue, and length of return on investment.
The initial funding for the
development of sail modules through the prototype and testing stages
would probably need to come at least in part from governments firmly
committed to the reduction of carbon emissions. The international
research institute that has been proposed by the OPRF might be a
suitable body to coordinate this process [3]. The major class
societies ABS, Lloyd’s Register, and Det Norske Veritas will also be
key elements in encouraging the required innovation.
When a suitable design has
been achieved, then there is the potential for the rig modules to be
provided and serviced by companies on a leasing basis to the ship
operators. This approach would remove from the ship operators the
initial capital investment required for module development, and
allow them to focus on the potential for fuel conservation and the
cost of adapting their ships to accept the sail modules. The leasing
costs could be linked to the savings achieved in such a way that the
ship operators have a financial incentive to adopt wind assistance
while the income to the leasing company is also sufficient for
long-term viability.
With the sail module
approach, risks are therefore reduced by removing development costs
from the ship operators, by leasing the modules on an as-needed
basis, by carrying out servicing and repairs with the modules on
land, by operating the sails remotely from the bridge without the
need for crew members to take risks, by having redundancy in
multiple rigs, and by their ability to be folded away to deck level
when not required. It is hoped that these qualities of sail modules,
together with the growing pressures for shipping to become more
sustainable, will encourage uptake.
Sails and other forms of
wind propulsion obtain energy from a free and sustainable source,
albeit a variable one, and with the exception of their manufacture
and decommissioning these technologies have minimal impact on the
environment during their use. The experience gained with the sail
module system proposed here will be of benefit to designers of
next-generation ships, perhaps encouraging the incorporation of
folding rigs during the design process.
5. CONCLUSIONS
The sail module proposal
offers a practical approach to wind assistance for commercial
vessels, complementing other approaches such as kite and rotor
propulsion. It has the advantage that it can be developed and
implemented over a relatively short time scale since it draws upon
generally well-understood principles and practice and can be applied
to a proportion of existing ships. It can therefore help to improve
the sustainability of the shipping industry over the shorter term
while more radical designs are developed for the next generation of
ships. It will be possible for ship operators to achieve commercial
benefits by the adoption of this form of wind assistance.
6. ACKNOWLEDGEMENTS
I wish to acknowledge
funding from the National Endowment for Science, Technology and the
Arts (NESTA) for development of the Transition Rig concept in
2000-2001.
7. REFERENCES
1. GREENWAVE,
www.greenwave.org.uk/GreenwaveBrochure.pdf
(accessed 1 February 2010).
2. THE NAVAL ARCHITECT,
Editorial: ‘Where to now, guv’nor?’, The Naval Architect, 7,
January 2010.
3. THE NAVAL ARCHITECT,
Editorial: ‘United we stand’, The Naval Architect, 50,
January 2010.
4. IPCC, ‘IPCC Climate
Change 2007’, Cambridge: Cambridge University Press, 2007.
5. SCHIEMEIER, Q., ‘The real
holes in climate science’, Nature, 463, 284-287, 2010.
7. THE NAVAL ARCHITECT,
Editorials: ‘Orcelle: pioneering a pure green revolution’, and
‘Orcelle: a totally green concept for the future’, The Naval
Architect, 3 and 14, April 2005.
8. SPYROU, A., ‘Quest for
fossil-free commercial ship propulsion’, The Naval Architect,
41, May 2005.
9. SOLAR SAILOR,
www.solarsailor.com (accessed 1 February 2010).
10. B9 SHIPPING,
www.b9shipping.com (accessed 23 January 2010).
12. HARRISON, D., ‘Unveiled:
the clean queen of the sea’, The Sunday Telegraph, 11, 13
March 2005.
13. THE NAVAL ARCHITECT,
Editorial: ‘Cup could run over for Aquatankers’, The Naval
Architect, 184, September 2007.
14. CUTTY SARK,
http://en.wikipedia.org/wiki/Cutty_Sark (accessed 30 January
2010).
15. CARTER, C.J.M., ‘Grain
for the Mersey in square-riggers’, Shipping - Today & Yesterday,
13-17, June 2005.
16. GLENN, D., ‘Flight of
the Falcon’, Yachting World, 71-80, January 2007.
17. SCHWAB, H-B., ‘21st
century sails: pollution-free propulsion systems’, In: Marine
power and propulsion: solutions for naval architects, Supplement
to The Naval Architect, 18-20, October 2005.
19. NAAIJEN, P.,
‘Performance of auxiliary wind propulsion for merchant ships using a
kite’,
www.icmrt07.unina.it/Proceedings/Papers/c/26.pdf (accessed 12
january 2010).
20. CMTV,
http://www.ctmv.eu/ (accessed 24 January 2010).
21. PELMATIC KNUD E. HANSEN,
‘Modern Windships, Phase 1’, Copenhagen: A/S, 75, Bredgade,
DK-1260, 1996.
22. PELMATIC KNUD E. HANSEN,
‘Modern Windships, Phase 2’, Copenhagen: A/S, 75, Bredgade,
DK-1260, 1999.
23. DRYDEN, R., ‘Proposal:
modular sailing rigs to provide wind assistance for larger vessels’,
The Naval Architect, 112-114, September 2004.
24. DRYDEN, R., ‘Transition
sailing rig’, Catalyst, 14-20, October 2004.
25. TRANSITION SAILING RIGS,
www.transitionrig.com (accessed 1 February 2010).
26. CROW, P., ‘The influence
of soils and species on tree root depth’, Forestry Commission
Information Note, 078, 2005
www.forestry.gov.uk/pdf/fcin078.pdf/$file/fcin078.pdf (accessed
28 January 2010).
27. TRIRIG VIDEO,
http://www.transitionrig.com/videos.htm (accessed 28
January 2010) .
28. GERNEZ, E., ‘Wind
propulsion for ships’,
www.admiroutes.asso.fr/larevue/2009/95/windpropulsionforship.pdf
(accessed 10 January 2010).
Richard Dryden
|